AB Engine Technology and
Technology Applications
This section describes several
possible design realizations of the fuel efficient AB Engine depending
on the Internal
Combustion Engine (ICE) application. We would like to emphasize
that independent of which design solution is implemented, the AB
Engine Method will create the most fuel efficient ICE engine
theoretically possible! AB Engine is similar in fuel efficiency to
the Atkinson engine, but does not have the disadvantages of
implementing a complex mechanical solution. The AB Engine method
also delivers many “collateral” advantages beyond the
improvement in fuel efficiency such as low noise or silent
engines, low temperature and pressure exhaust gases (eco
friendly), linear power output with respect to RPM as well as
adaptable solutions to different fuel types and intake gas
conditions.
Watch it
on YouTube
The main idea protected by patent consist of two parts.
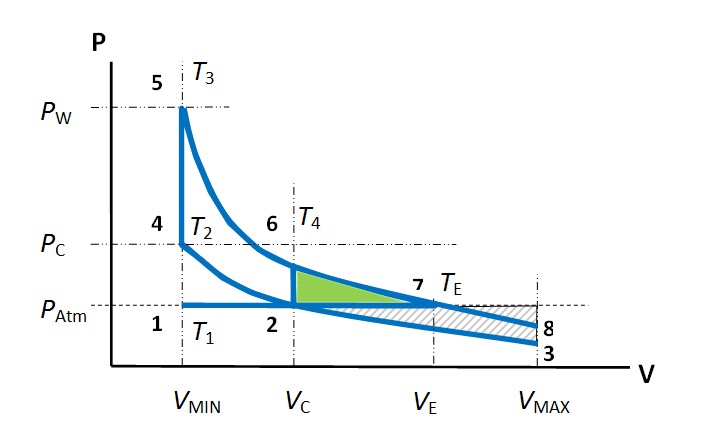
-
Ratio
of maximum chamber volume to the minimum R=VMAX/VMIN is
higher than critical volume VC for
particular fuel type. Definition of critical Volume is given in US
patent first claims#8,086,386
It is important to understand that R is not
theoretically limited, it can be as high as desired from fuel
efficiency point of view for one cycle at maximum power output.
Practically, it is limited by the ratio at which the expanding
burnt gas-fuel mixture reaches the environmental exhaust
pressure PATM at
volume VE. and temperature TE The
ratio R can be even higher for engine designs that utilize
different kinds of fuel.
-
Engine designs
that utilize the second part of the method admit oxidizing gas to
the combustion chamber with a gas mass that is less than equivalent
to “Critical Volume - VC”
at initial gas temperatureT1 and
pressure PATM.
P-V Diagram
(on the right) shows The "Alexander Bakharev (AB) engine P-V Cycle" of
ICE at maximum power output. Diagram is outlining conventional engines
(Otto, Diesel) cycles 1-2-4-5-6-2 and
AB Engine Cycle 1-2-3-2-4-5-6-7-8-7
Green area 2-6-7 represent
additional power generated by AB Cycle compare to conventional engine
defining higher AB engine fuel efficiency
Some possible design
solutions:
Solution 1.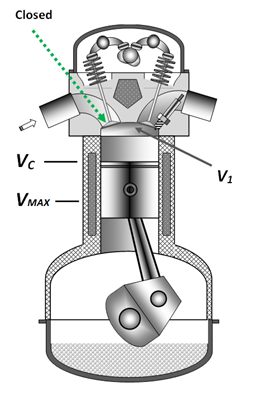
Engine design with fixed high pressure
Intake valve closing at a fixed level allowing gas intake below Critical
volume. This solution is well described in the patent with step by step
analysis of the Thermodynamics behind the method. (Picture bellow)
Applications: Excellent
solution for stationary or mobile power generators such as:
- Houses or offices
- Boats, yachts and large
ships (marine applications)
- Hybrid solutions for cars and
trucks
Advantages:
- The most inexpensive
implementation of the AB Engine Method and does not require the
design of unique engine parts.
- Excellent Design for an ICE
in Power generators with fixed
RPM and
particular fuel type.
Disadvantages:
All the disadvantages of ICEs with
fixed intake valves such as:
- Declining power output with
increase in RPM; this is not a disadvantage for Power Generators
since they can be designed and optimized for a particular engine
RPM.
- Inability to adjust actual
compression ratio to particular type of fuel or intake gas
temperature and pressure.
Solution 2.
Engine design with Time Variable
Valve (TVV)
This is a solution that requires
almost no changes to an existing engine that is already equipped
with TVVs and PC controllers. There is a need however to reprogram
the controller for specific parameters (variables) that are
essential for executing the AB Engine Method. It is also necessary
to implement sensors such that measure: temperature, pressure, RPM,
fuel type, combustion chamber and piston positions. Many sensor
solutions are already used in modern day technologies and they can
be adapted to the AB Engine Method.
Applications:
This is an excellent solution for
cars, motorcycles, trucks, airplanes and mobile Power generators
ICEs. This variant is suited for extreme weather conditions and
large altitude and atmospheric temperature/pressure changes.
Advantages:
-
Excellent for extreme weather
conditions and large altitude and atmospheric
temperature/pressure changes.
-
The TVV and PC controller
make this solution adaptable to almost any type of application.
-
Great engine dynamics
-
Easy to adapt to any fuel
type
-
Engine can start up with
gasoline and continue with Diesel
-
Easy to adapt to an existing
TVV technology
Disadvantages:
|
|
Solution
3.
Engine design with an AB Engine
Controlled Valve or Damper. This
solution is well described in the section of "Technology
Presentation" with
step by step analysis of the P-V diagram behind the method.
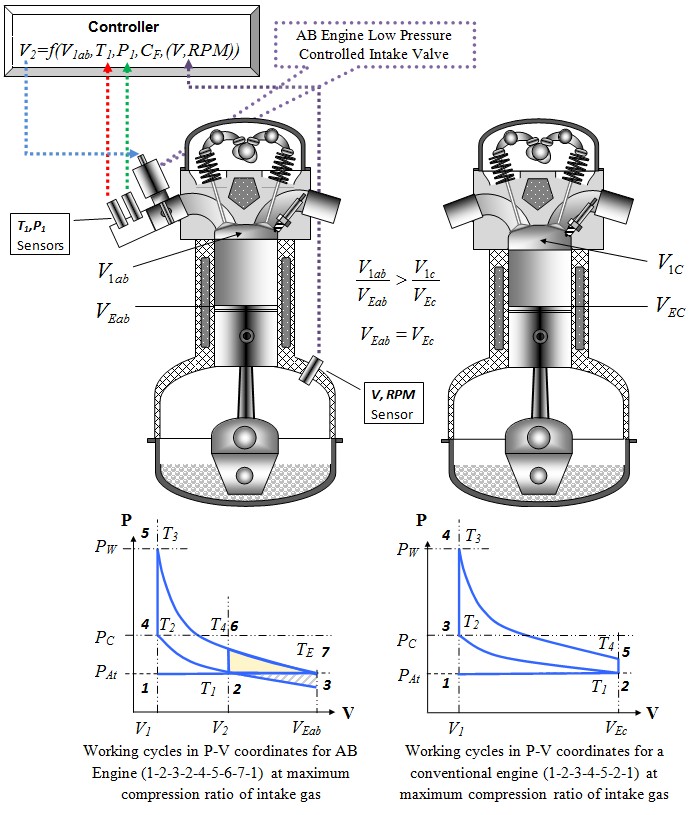
This is one of the AB Engine team's
favorite solutions. This technology is similar to TVVs, but has a
different and unique implementation. This technology is described in
detail in our ‘Technology Presentation” section, but there we did
not disclose all the advantages of this variation.
Applications:
This is an excellent solution for
cars, motorcycles, trucks, airplanes and mobile Power generator ICEs.
This variant is also suited for extreme weather conditions and large
altitude and atmospheric temperature/pressure changes. THe solution
is also adaptable to almost any type of application.
Advantages:
- This solution will provide the highest fuel efficiency
theoretical possible for internal combustion engine
- AB Engine Valve-Damper is applicable to single piston or
multiple piston engines. One of the great advantages of this
implementation is works with “normal” pressures and temperatures
of intake gas which simplifies the valve control and allows for
inexpensive solutions such as electromagnets for example.
- It simplifies the
valve-damper design because it combines two functions, it can be
used as a valve that opens and closed at specific times and
piston locations or
work as a damper creating gas flow resistance at higher engine
RPM.
- Excellent for extreme weather
conditions and large altitude and atmospheric
temperature/pressure changes. The solution is also adaptable to
almost any type of application.
- Great engine dynamics
- Easy to adapt to any fuel
type
- Engine can start up with
gasoline and continue with Diesel
- The best feature of the AB
Engine Valve-Damper is that multi-piston engines would only need
one valve at the manifold entrance. When acting as a damper it
creates gas flow resistance and ensures optimal actual
compression for any kind of fuel or intake gas condition. For
many ICE applications it is possible to use Valve-Damper without
PC controller adjusting fixed Damper position manually for
particular fuel type or "summer-winter" intake gas conditions. I
would separate it as a Solution
4. This
solution is excellent, but
not limited, for
engines working with constant RPM.
Disadvantages:
The AB Engine team does not
see any significant disadvantages in using an AB Engine
Valve-Damper. As this is a highly flexible solution, there is no
need to implement it in more rigid ICE applications such as
those described in solution one, that is, low power house
generators etc...
|